About ecca
The European Coil Coating Association (ECCA) is an international non-profit association dedicated to the promotion of the use of prepainted metal as the environmentally sound, the cost effective and the high quality method of finishing.
Coil coating lines in Europe (STS BREF 2020)
since 2008, we have reduced our fossil fuel-based CO2 emissions.*
industrial and commercial buildings in Europe use prepainted metal annually.*
35% energy consumption reduction since 2008
Our market is now 3x the size it was in 1992.* ECCA Statistics
We produce 1.5 billion sq.metres of product each year* Enough to cover 200,000 football pitches.
Over 100 infinite colours and finishes.
*ECCA Statistics & Benchmarking
About Coil Coating
The coil coating process which is used to produce prepainted metal is continually evolving to produce better products, higher quality, faster and with lower environmental impact. Some of the major innovations in recent years have been:
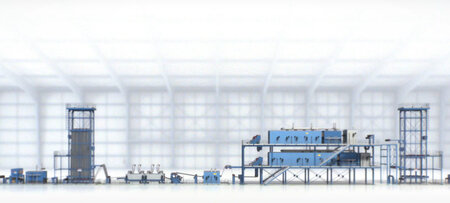
The basic technique of applying paint by roller coating is at the heart of prepainted metal and continual innovation is used to make this faster, more consistent and more efficient
The adoption firstly of reverse-cascade rinsing and then of no-rinse pre-treatment on many coil coating lines has dramatically reduced water usage in the initial stages of the process
The most energy-intensive part of the coil coating process has seen major development to provide more efficient ovens, able of curing paint in seconds, using both traditional gas-fired techniques, but also innovative induction, IR/NIR, UV/EB curing techniques
The coil coating process allows for very efficient collection of VOCs from the solvents used in paints and the latest oxidisers ensure that over 99% of these are destroyed without polluting the atmosphere.