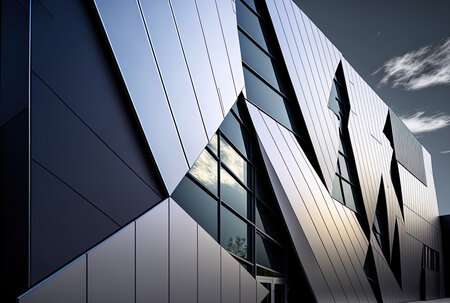
The case for prepainted metal
There are multiple reasons to opt for prepainted metal products over alternative materials and coating processes. Design flexibility and the simplicity of realisation of designs through the fabrication and manufacturing process are key advantages. Prepainted metal products also perform extremely well in terms of environmental impact and sustainability.
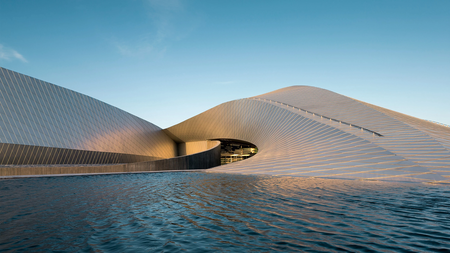
Advantages in design
Prepainted metal provides a high-quality painted surface in a spectrum of colours and different textures. The surface can be matt or high gloss, smooth, orange-peel or embossed. You can also add printed films to create effects such as woodgrain.
Availability in all the usual steel and aluminium grades and alloys means you can balance formability, strength and appearance in the final product.
Detailed independent life cycle assessment (LCA) shows the environmental impact of prepainted metal is less than that of post-paint metal across a wide range of impact categories. Prepainted metals are also easily recyclable, making them the clear choice for sustainable design.
Although the organic coatings used in coil coating are generally thinner than postapplied powders and films, they still give better in-service performance. So, you use less paint, which minimises resource consumption and enables you to cut down or even eliminate maintenance and re-painting.
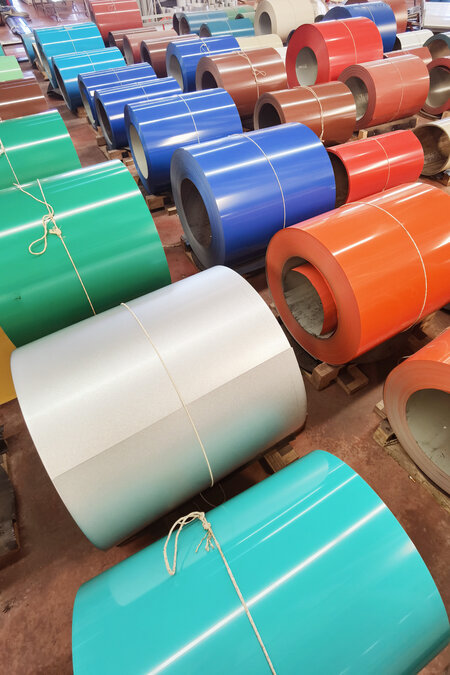
Process advantages
The continuous coil coating process gives the highest standards of quality assurance through coil to coil consistency and has a significantly lower environmental emissions than batch or post-painting processes.
Operated in accordance with the latest national and European standards for VOC emissions and emissions to water, this environmental compliance means that prepainted metals are a material of choice in a wide range of applications.
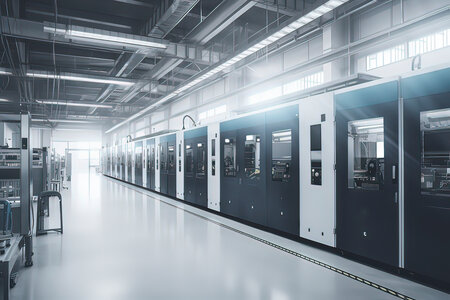
Production cost reduction
By using prepainted metals, manufacturers are able to eliminate their paint lines, which are typically a major bottleneck in their operation. Capacity constraints are also minimised, potentially improving ROCE.
At the same time, the cost of complying with environmental regulations is significantly reduced or eliminated, as are the costs of hazardous waste disposal associated with the painting operation.
Since input material is more directly related to output, processing time is reduced, while scheduling problems and costs associated with batch-type processing are also minimised or removed altogether.
The consistent quality of coil coated materials reduces the need for re-work and lowers non-conformance levels and associated costs. Ultimately, using prepainted metal allows manufacturers to concentrate on core competencies, freeing up resources and easing pressure on production processes.