Prepainted metal for
designers
Designing with prepainted metal is very similar to designing with any other form of sheet metal, but with the additional advantage that the product already has the required surface aesthetics.
There are, however, a few characteristics of prepainted metal which the designer should consider to ensure a successful final product. Much of this stems from the fact that the paint finish is present before forming.
Coatings used on prepainted metal have been formulated to flex with the base metal. Since different levels of flexibility are available, it is critical you select the right prepainted product at the start of the work.
Prepainted coatings typically retain their adhesion, even at a 0T bend radius, but you will need to confirm this before starting the design.
While the coatings are standardly formulated to be very scratch resistant, a range of textures and hardness profiles are available. We recommend checking with your supplier to identify the most appropriate product.
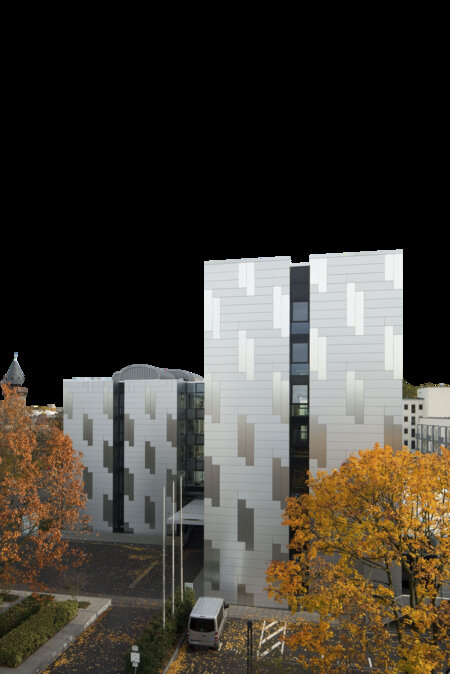
Production guidance
When assessing the tooling to be used for forming operations, it is important to remember that a scratch in forming is a scratch on the finished product. But any issues can usually be overcome with good quality tooling, good design and (if necessary) using a temporary protective film.
You should also keep in mind that the finish is applied before any joining takes place. Conventional welding could damage the surface appearance of the product. Fortunately, there are numerous modern joining techniques that are well established and can be used instead of welding.
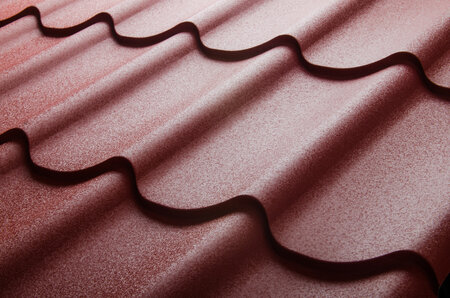
Forming prepainted metal
Most techniques applicable to sheet metal can be used successfully on precoated products. This includes shearing, blanking, press braking, bending and folding, roll forming, deep drawing, and spinning.
Because the prepainted product contains the final surface finish, it is important that the tools are in good condition with no scratches or damage on the tooling surfaces.
It may be necessary to modify contact pressures to avoid scratching, but usually a good clean and polish of the tooling is all that is required. Since prepainted metal is selflubricating, tools used for forming this material tend to stay clean and last longer.
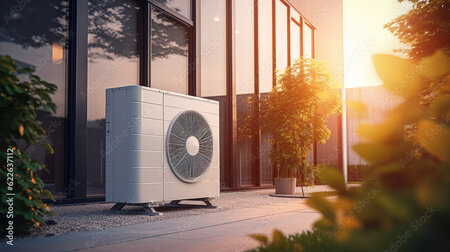
Finishing
The back of the prepainted metal sheet will usually have a different appearance to the front side.
This may be useful, for example, providing a simple grey coating for the inside of a filing cabinet, but you can also specify the same finish on both sides.
Another point to consider is that at least two edges will be uncoated, since they will have been cut from a much larger metal strip. Bare edges can look unattractive and (worst case) be the initiation point for corrosion.
Again, there are well established techniques for treating these edges in the final product to deliver the desired outcome.
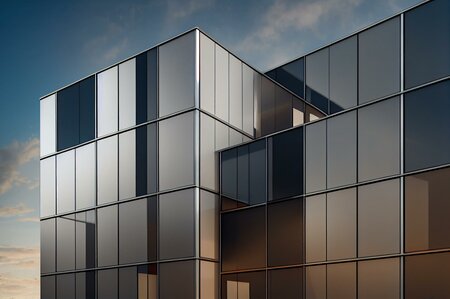